For Building Services, the lower the system efficiency, the higher the cost will be to achieve the desired specified design criteria, ie room temperature etc
The efficiency of even the best designed systems can be undermined by incorrect product selection and installation.
System efficiency depends on several factors, which include;
- Design
- Installation
- Product selection
- Commissioning
- Maintenance
Design, installation and maintenance are influenced by the process of selecting suitable consultants, contractors and FM company.
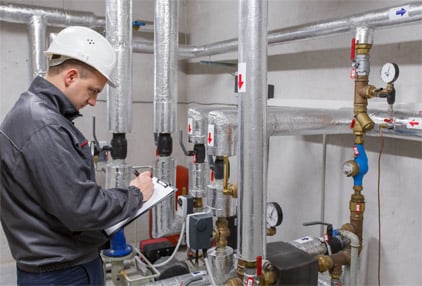
System Selection
Crane Fluid Systems are of course happy to review and advise on system design and installation, as correct product selection / placement and commissioning are fundamental to energy efficiency. Please use our knowledge and experience in these key areas.
Correct selection and installation of control and commissioning valves not only ensures correct flow rates and as a consequence, terminal unit heat output, but also impacts the boiler/chiller efficiencies and Pump running costs
Efficiencies
If we first consider the boiler/chillers, we know that the efficiency depends on maintaining the correct at (differential temperature), ie the difference between flow and return water temperatures at the boiler/chiller.
For boilers the relevant at will vary depending on fuel type, eg oil / gas / heat pump etc. For condensing boilers to work correctly, the return water temperature has a major impact on boiler efficiency.
For chillers, the design at is maintained by control over the return water temperature.
Control over the return water temperature, therefore controlling the at, is therefore key when considering system efficiency for both boilers and chillers.
Running Costs
Pump running costs are influenced by;
- Actual efficiency of the selected pump
- Flowrate
- Resistance to flow within the system, ie the pump head required to circulate the water
The efficiency of the pump depends on pump design and operational area on the pump curve, as shown in the adjacent chart
Required flow rate will be dictated by design depending on heat loss / gain and terminal unit type within the building. The mass (total) flowrate is the sum of all the individual flow rates to all the terminal units. Diversity (CIBSE CP1) is used more frequently now in system sizing so the mass flow rate may be lower than the sum of terminal flowrates.
Variable Flow
With variable flow system design, the flowrate and therefore the resistance to flow, ie the ‘effort’ that the pump needs to generate the required flowrate, will vary depending on demand for heating / cooling, which will of course vary throughout the day; week; month; year.
An example of savings in pump running costs, for either heating or chilled systems, might be;
- Demand reduces flowrate (terminal unit heat output) requirement by 50%
- Variable speed pump slows to match new flowrate requirement
- Resistance to flow reduces to 25% at 50 % flow rate
- Squared relationship between flowrate and resistance to flow
- Flowrate reduces to ½, resistance reduces to 1/4
- Pump energy consumption reduces to 12.5% at 50% flow rate
- Cubed relationship between flowrate and energy consumption
- Flowrate reduces to ½, energy reduces to 1/8
The control over fluctuating pressure, caused by ever changing flowrate requirements, is fundamental to system efficiency.
The correct selection and installation of DPCVs (Differential Pressure Control Valves) and PICVs (Pressure Independent Control Valves) is an integral part of installation process and is therefore essential to achieving an energy efficient HVAC system.