Imagine attending an emergency call at one of your sites, only to find the building flooded and a critical component partially cracked – or even completely separated – at the site of the flood.
Immediately, you would assume that the part had failed — and in some capacity, it has.
However, the mechanism of failure — how the material failed and why it reached that state – may not be quite so black and white. If you have ever had the unfortunate experience of having one of your installations go catastrophically wrong because of part failure, stress corrosion cracking may well be the culprit.
Three factors are required for stress corrosion cracking to occur: a susceptible material, that is exposed to some level of applied stress and a corrosive species within the heating system (such as a substance or liquid), causing a crack to form within the material.
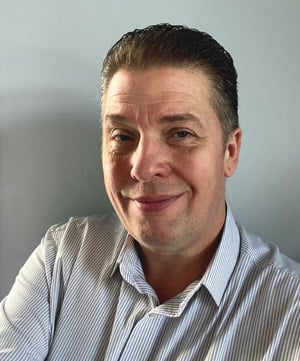
By Darren Westwood
Group Quality Manager
Crane Building Services & Utilities
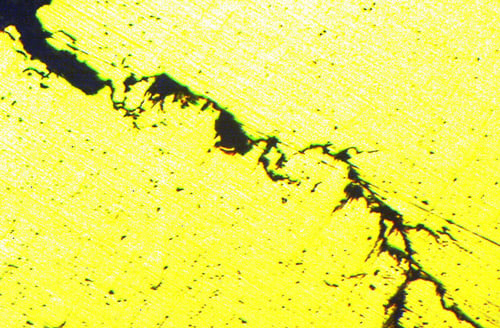
An example of fine branch cracking within a material, which is indicative of stress corrosion cracking.
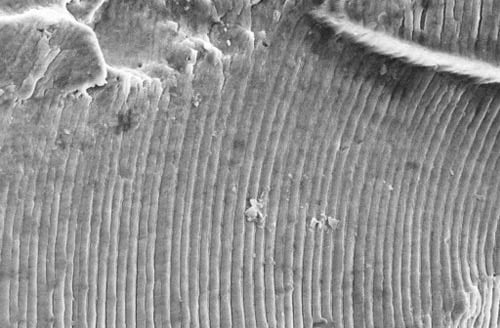
Fatigue striations are present when a material has failed, which are noticeably different to stress corrosion cracking.
At first, these cracks are very small, embryonic fractures that can only be seen under a microscope, called branch cracking.
When that part is then subsequently placed under further stress, the material cannot cope with the additional loading and the material fails, often suddenly and disastrously, However, this type of failure is not the same as a part being manufactured to poor quality standards. Instead, it is usually caused by an additive being used within a system which is incompatible with the pipes and fittings.
A metallurgist can identify the different failure mechanisms through the different patterns that are caused within the material. A material fatigue failure, for example, will have a clamshell pattern with fatigue striations, which indicates the cyclic nature of fatigue and creates a visibly different crack to the fine branch cracking caused by stress corrosion cracking.Â
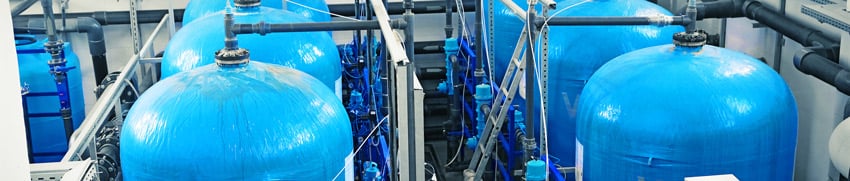
Often, this type of failure happens with copper and copper alloy (brass and bronze) valves, as these materials are susceptible to corrosion. Every installation that joins two parts together will be subject to some stress, so all that is required to create the perfect conditions for stress corrosion cracking is a corrosive substance. One of the most commonly used additives for system dosing* that has been a factor in many cases of stress corrosion cracking is silver peroxide.
In recent years, there has been an increase in the use of this additive for system sanitisation purposes as stainless steel pipework has become more widely used. Typically, silver peroxide works well with stainless steel systems. However, often there are many copper fittings within the pipework system. Once copper has been exposed to this substance, the corrosion process begins and cannot be stopped, even if the system is flushed. If this happens, it is just a matter of time before stress corrosion cracking causes a failure in one of the fittings. Unfortunately, at this stage, the only way to avoid a part failure would be to replace every copper fitting.
Knowing which additives and substances are compatible with the parts you wish to use is difficult. In addition to the wide range of different chemical compounds that are available, there is the added complication that some chemicals can be used safely with materials within certain temperature ranges. While an approved list of chemicals for use within the plumbing and heating industry is gaining traction, for now, the only way to be sure you are using compatible chemicals and materials is to check with the manufacturers of both the part and the chemical.
*For more general guidance on pre commissioning cleaning of pipework systems, refer to BSRIA BG29/2020.
Additives & Substance Compatibility Guide
The use of substances such as silver peroxide (a combination of silver nitrate and hydrogen peroxide) can severely destabilise copper and copper based alloys to the point of catastrophic failure.
It must be ensured that the dosing chemicals are correct for the application.
Download full chart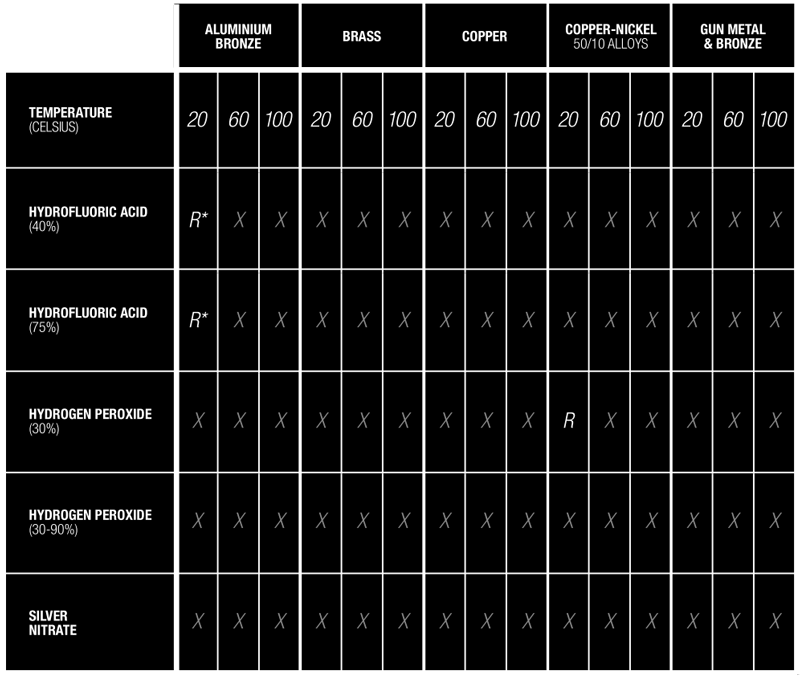
As featured in BSS Solutions magazine – December 2020